Sign up for The Media Today, CJR’s daily newsletter.
When Joel Birket was a child, his family moved to new cities for a year at a time so his father, William, could install printing presses at the major daily newspapers in Seattle and Minneapolis. “I saw all the different trades and effort that was put into making these presses work,” Birket says. “It was just fascinating.” Later, Birket—who entered the same line of work in 1994, and who now oversees his own shop specializing in machinery moving and press installations—opened drawers at printing plants and spotted his dad’s handwriting on old drawings detailing the operations of a press.
Recently, Birket, who is 44, stood in the press room of the Nashville-based Tennessean for a different sort of job than the one his father so often performed. In 1989, Birket’s dad had installed the Tennessean’s printing press. Nearly three decades later, Birket had returned to take it apart.
New at CJR: With Ink, a knowing audience encounters a young Murdoch
Unlike his father, who died in 2015, Birket spends more of his time dismantling presses rather than installing them. Faced with declining circulation and advertising revenue, an increasing number of newspapers, most of which used to have a press in a backroom or basement, have outsourced their printing to a central location serving multiple newspapers. In some cases, the newspapers hire companies to simply demolish the presses and haul them away. In others, they locate other publications interested in the equipment. For the latter, they hire Birket, who carefully takes the press apart and then transports parts of it.
A typical press, Birket says, is 160 feet long and weighs 1,000 tons, and machinists must align and level it within 3/1000 of an inch in order for images to appear cleanly on newspapers. Successful installation requires meticulous mechanical work as well as electrical and plumbing skills, which many people in the printing-press industry learned on the job, according to Jason Birket, Joel’s older brother.
“It’s a unique job—there were only a few people in the world who did it,” Jason Birket says. Like his brother and their father, Jason Birket worked for Goss International, one of the largest printing-press manufacturers in the world. His first press installation, as an apprentice machinist, was at the Tennessean in 1989. Combined, the three Birkets installed hundreds of printing presses around the world.
“There is no formal school—you can’t go to a university or college to learn how to install a printing press,” Jason Birket says. “Those of us who did it working for Goss always say that we went to the University of Goss.”
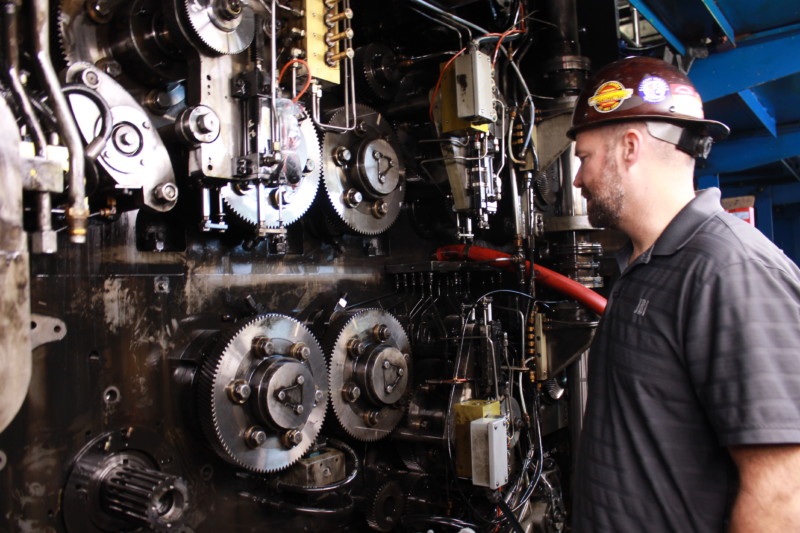
Joel Birket looks at a gear box, which controls the mechanical parts of the printing press at the Tennessean. Photo by Eric Berger.
At the Tennessean, engineers designed the printing equipment, which occupied the bottom floors of a 50,000-square-foot building, to flawlessly create thousands of copies of each issue—“fold them and cut them, 70,000 an hour, spit them out all in one line, right on a conveyor, right into a mailroom,” Joel Birket says. Most newspapers no longer need that capacity. The total circulation of daily US newspapers declined from 62.3 million in 1990 to 30.9 million in 2017, according to a Pew Research Center report. News & Tech tracked printing plant closures from 2004 to 2015, but has since stopped. Many news outlets don’t publicize the closures of their own presses, which makes tracking such closures an inexact science, Mary Van Meter, publisher and editor-in-chief of News & Tech, says. Every few weeks brings news of another paper closing its printing plant.
It was a comforting sensation. I listened for it every day. It was affirming in a way I could not explain.
Last year, The Tennessean, part of the Gannett-owned USA Today network, announced the impending closure of its in-house pressroom, timed with the paper’s move to a new office. Printing operations for the paper would shift 180 miles east, to Knoxville—a move the paper estimated would end the jobs of 30 pressroom workers. “Nashville’s loyal pressmen face their final deadline,” read one Tennessean headline about the transition. A North Carolina-based real-estate developer bought the Tennessean property for $50.3 million and, according to the Nashville Post, plans to demolish the paper’s building.
In February, the paper hosted “The Legacy of 1100 Broadway” at its offices. During the event, Leon Alligood, a former Tennessean reporter who now teaches at Middle Tennessee State University, recalled how the life of the printing press assured him during his time at the paper. “It was a comforting sensation,” he recalled at the event. “I listened for it every day. It was affirming in a way I could not explain.”
Dale “Duke” Welsh, director of operations for Ultimate Marketing, a company that specializes in “asset recovery of newspaper press and electronic part,” has in recent months visited six Gannett newspapers, including the Tennessean, to oversee the transfer or sale of printing press parts from one plant to another. He says he keeps his distance from longtime printing plant employees when he enters a job site.
“The first week is always eerie,” says Welsh, whose father and grandfather also worked on printing presses. The Tennessean press printed its final issue in Nashville on Sunday, March 3, and featured pressroom employees on the front of a section. “I was here on Monday morning,” says Welsh. “So when they see me coming, it’s like, ‘It’s real now.’”
Birket must clear the press equipment out of Nashville by May. Later this year, he’ll install it at The New York Times, whose printing operation in Queens also prints USA Today, Newsday, and AM New York. David Stenstrom, who is the Times pressroom general foreman, says the Times wants to increase its color-printing capacity.
“Obviously, there is quite a bit of used equipment on the market, so it’s not a bad deal,” Stenstrom, a third-generation pressroom worker who started at the Boston Globe in 1976, says. “We are looking at where we need to invest to make ourselves a more profitable printer and provide printing for other products.”
Jason Birket, who lives in Florida, now works for the Times as a regional production manager. Though the Times gives a new life to the Tennessean’s press and saves it from the scrapyard, Jason believes press installers will go the way of “watchmakers or typewriter makers.”
Joel Birket has already started to move his own business into other areas. He offers rigging services and makes and repairs machine parts for manufacturers such as Nissan and Schneider Electric. His work at The Tennessean coincided with spring break for his 15-year-old son, Mason. Birket hired Mason to clean ink pans at the paper, and was happy with his son’s work. Since then, his son has asked for more hours in the family business, though of course Birket can’t say how long that work will involve printing presses for newspapers.
“I hate to see these presses go because I knew the people who ran the presses and maintained the presses, and they had families they supported based on this industry,” Joel says. “You could come into a newspaper and get a job and have it be a career. I hate to see careers go away, but it’s just evolution and change.”
The Media Today: Myanmar court confirms Reuters reporters’ sentence
Has America ever needed a media defender more than now? Help us by joining CJR today.